在選擇齒輪淬火方式時(shí),超高頻淬火和中頻淬火各有其獨(dú)特的優(yōu)勢(shì)和適用場(chǎng)景。為了做出明智的選擇,應(yīng)綜合考慮以下幾個(gè)關(guān)鍵因素:
一、齒輪的尺寸與厚度
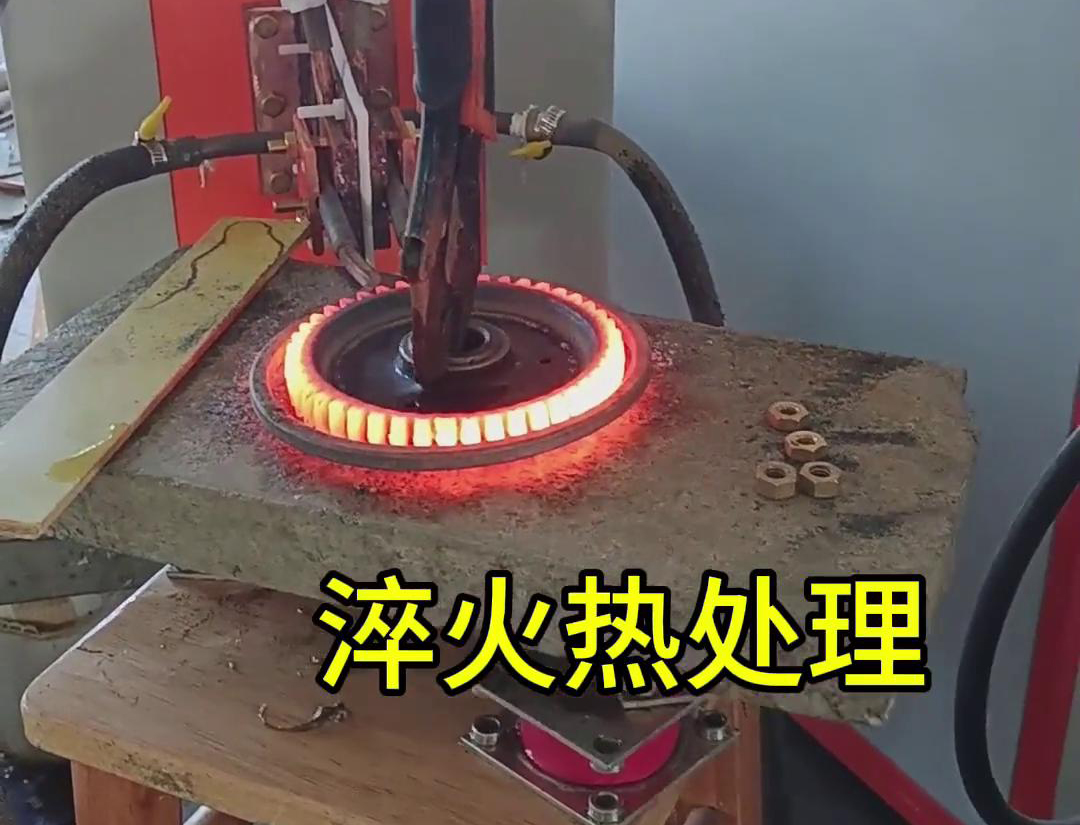
二、淬火層深度要求
- 超高頻淬火:適用于較淺的淬火層深。超高頻的特性決定了它在齒輪表面能夠產(chǎn)生集中的熱量,使得淬火層主要集中在表面附近。這種淺淬火層對(duì)于一些只需要表面高硬度、耐磨性好,而內(nèi)部保持一定韌性的齒輪非常適用。
- 中頻淬火:適用于較深的淬火層深。中頻產(chǎn)生的磁場(chǎng)能夠使熱量深入齒輪內(nèi)部,形成較深的淬火層。這對(duì)于一些需要有足夠深的淬火層來承受巨大壓力和剪切力的齒輪應(yīng)用場(chǎng)景(如礦山機(jī)械、船舶推進(jìn)系統(tǒng)中的齒輪)更為合適。
三、淬火時(shí)間與加熱速度
- 超高頻淬火:加熱速度極快,能夠在幾秒甚至更短的時(shí)間內(nèi)將齒輪表面加熱到淬火溫度。這對(duì)于一些對(duì)淬火時(shí)間有嚴(yán)格限制的生產(chǎn)流程非常有利。
- 中頻淬火:相對(duì)來說加熱速度稍慢,但能夠在相對(duì)較長(zhǎng)的時(shí)間內(nèi)使齒輪整體溫度升高。這樣在淬火冷卻后,齒輪從表面到內(nèi)部的硬度變化相對(duì)較為平緩。
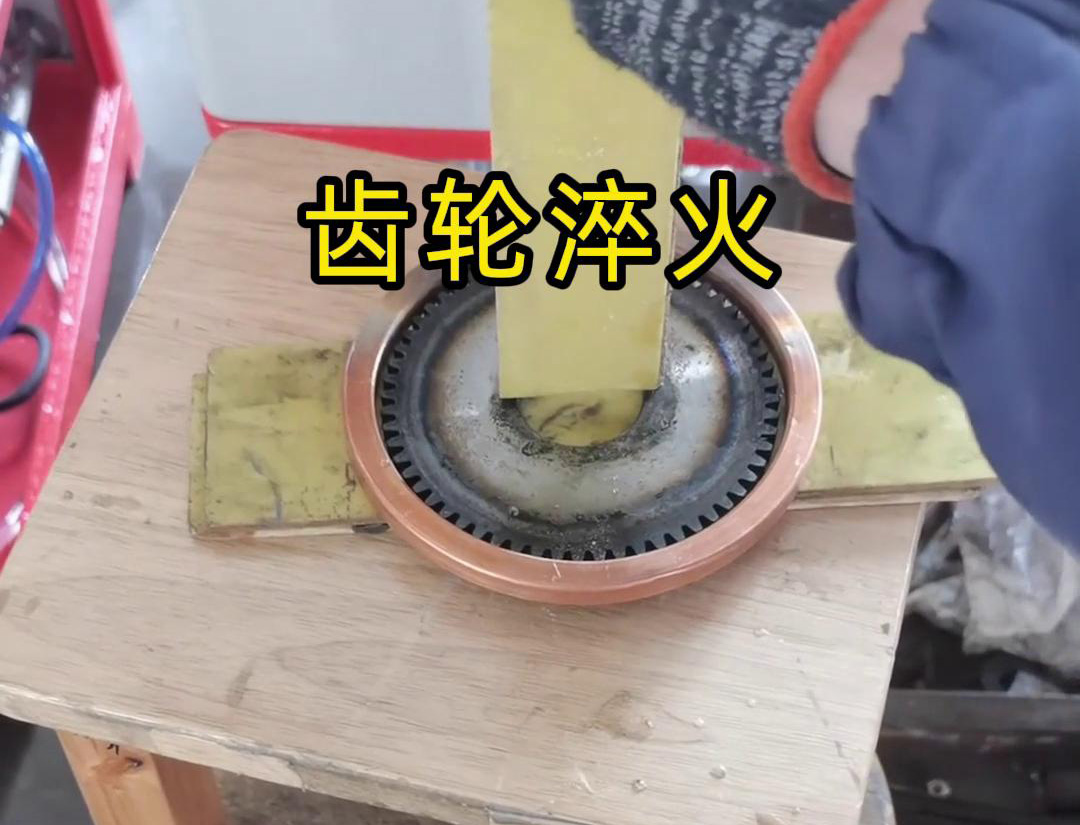
四、最終硬度與性能要求
- 超高頻淬火:淬火后的齒輪表面硬度通常較高,這是因?yàn)榭焖偌訜崾沟谬X輪表面的奧氏體化過程迅速完成,隨后的淬火冷卻能夠形成細(xì)小、均勻的馬氏體組織。這種高硬度表面對(duì)于抵抗齒輪表面的磨損和膠合等失效形式具有顯著的效果。
- 中頻淬火:在需要保持一定硬度梯度以平衡耐磨性和韌性的情況下是更好的選擇。它能夠在整個(gè)齒輪截面上保持一定的硬度分布,避免表面硬度極高而內(nèi)部硬度驟降的情況。
五、生產(chǎn)成本與效率
- 超高頻淬火:設(shè)備成本可能相對(duì)較高,但由于加熱速度快,可以顯著提高生產(chǎn)效率,適合大批量生產(chǎn)或需要快速淬火處理的場(chǎng)景。
- 中頻淬火:設(shè)備成本相對(duì)較低,適用于各種規(guī)模的生產(chǎn)。雖然加熱速度稍慢,但在保證淬火質(zhì)量的前提下,仍然能夠滿足大多數(shù)齒輪的生產(chǎn)需求。
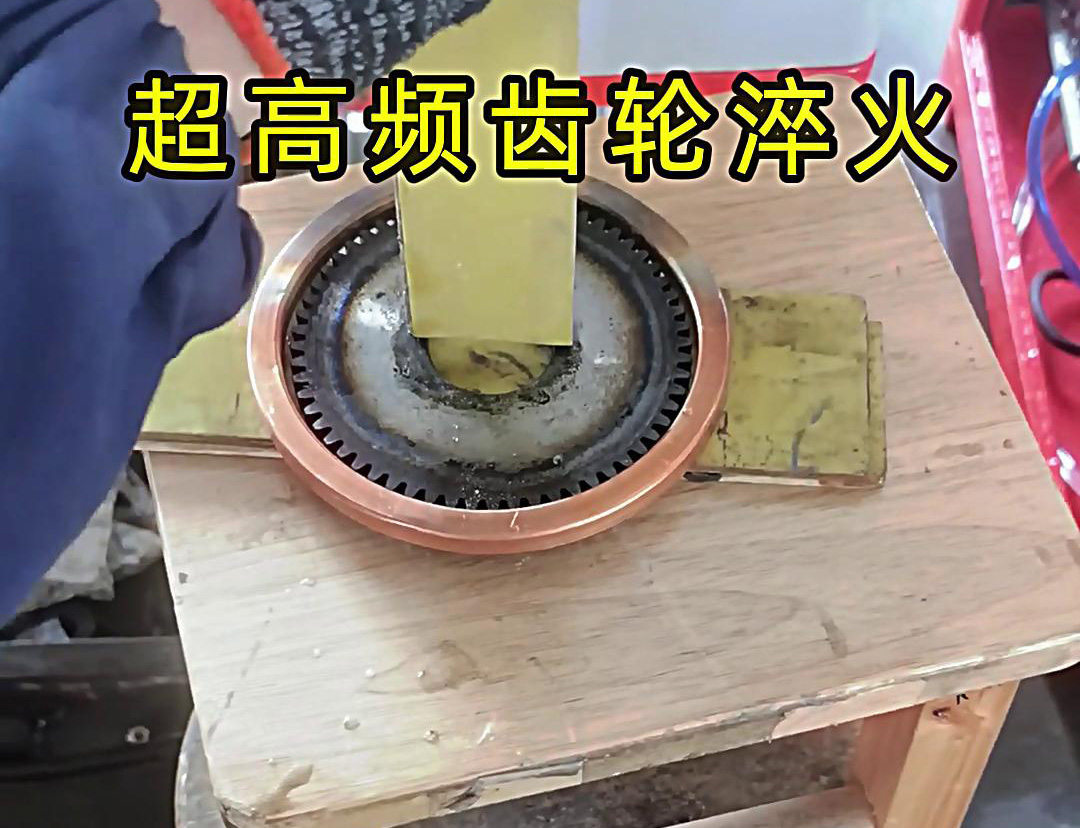
綜上所述,在選擇齒輪淬火方式時(shí),應(yīng)綜合考慮齒輪的尺寸與厚度、淬火層深度要求、淬火時(shí)間與加熱速度、最終硬度與性能要求以及生產(chǎn)成本與效率等因素。通過全面評(píng)估這些因素,可以做出最適合自己生產(chǎn)需求的淬火方式選擇。
|