凸輪軸高頻淬火是一種常見(jiàn)的熱處理方式,它利用高頻感應(yīng)加熱技術(shù),迅速將凸輪軸表面加熱至淬火溫度,然后快速冷卻,以提高凸輪軸的表面硬度和耐磨性。以下是對(duì)凸輪軸高頻淬火的詳細(xì)分析:
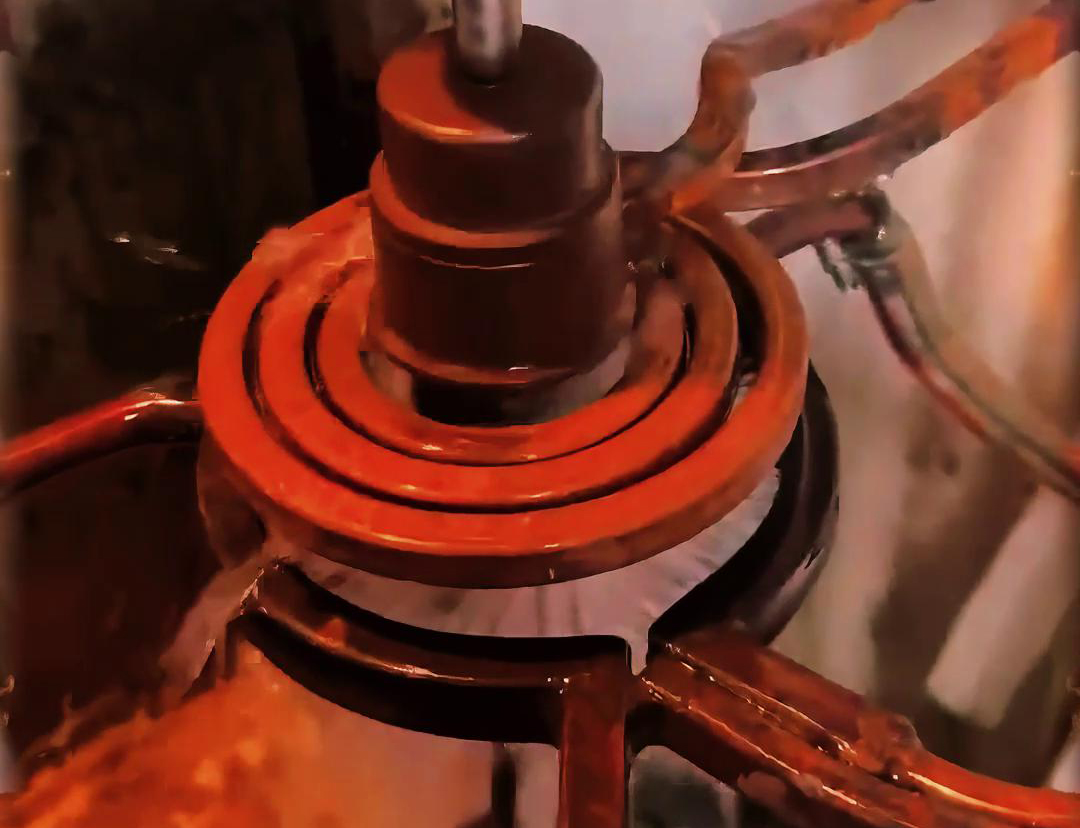
一、高頻淬火機(jī)床的構(gòu)成
- 加熱設(shè)備:采用高頻感應(yīng)加熱技術(shù),能夠迅速將凸輪軸表面加熱至淬火溫度。
- 淬火機(jī)床:支持凸輪軸的定位、夾持和淬火過(guò)程中的穩(wěn)定運(yùn)動(dòng)。
- 冷卻系統(tǒng):用于淬火后的快速冷卻,確保淬硬層的質(zhì)量和深度。
- 控制系統(tǒng):實(shí)現(xiàn)設(shè)備的自動(dòng)化操作,包括加熱溫度、淬火時(shí)間等參數(shù)的精確控制。
二、高頻淬火的優(yōu)勢(shì)
- 加熱速度快:高頻感應(yīng)加熱技術(shù)能夠在極短的時(shí)間內(nèi)將凸輪軸表面加熱至所需溫度,提高生產(chǎn)效率。
- 無(wú)氧化層:由于加熱過(guò)程中無(wú)需與火焰直接接觸,因此凸輪軸表面不會(huì)產(chǎn)生氧化層,保持原有的金屬光澤和性能。
- 硬度均勻:通過(guò)精確控制加熱溫度和淬火時(shí)間,可以確保凸輪軸表面淬硬層的硬度和深度均勻一致,滿足工藝要求。
- 自動(dòng)化程度高:現(xiàn)代高頻淬火設(shè)備通常配備先進(jìn)的控制系統(tǒng),能夠?qū)崿F(xiàn)手動(dòng)和自動(dòng)加熱功能,操作簡(jiǎn)便且節(jié)省人力資源。

三、高頻淬火工藝參數(shù)的選擇
- 加熱頻率:加熱頻率的選擇主要取決于凸輪的幾何形狀和淬硬層深度的要求。通常,加熱頻率越高,透入深度越淺,能量更集中,加熱效率也越高。在滿足淬硬層深度的前提下,應(yīng)盡可能選擇較高的加熱頻率。
- 功率密度:功率密度的大小直接影響加熱速度和淬硬層的質(zhì)量。根據(jù)工件尺寸和加熱要求,選擇合適的功率密度。
- 冷卻速度:冷卻速度對(duì)淬硬層的質(zhì)量和深度有重要影響。冷卻速度過(guò)快可能導(dǎo)致淬硬層過(guò)淺或產(chǎn)生裂紋,而冷卻速度過(guò)慢則可能導(dǎo)致淬硬層過(guò)深或產(chǎn)生軟點(diǎn)。因此,應(yīng)選擇合適的冷卻速度以確保淬硬層的質(zhì)量和深度。
四、高頻淬火的應(yīng)用范圍
高頻淬火廣泛應(yīng)用于各種軸類零件的表面淬火處理,包括但不限于汽車凸輪軸、傳動(dòng)軸、搖臂軸等。這些零件在機(jī)械設(shè)備中需要承受較大的載荷和磨損,通過(guò)高頻淬火處理可以提高其表面硬度和整體性能。
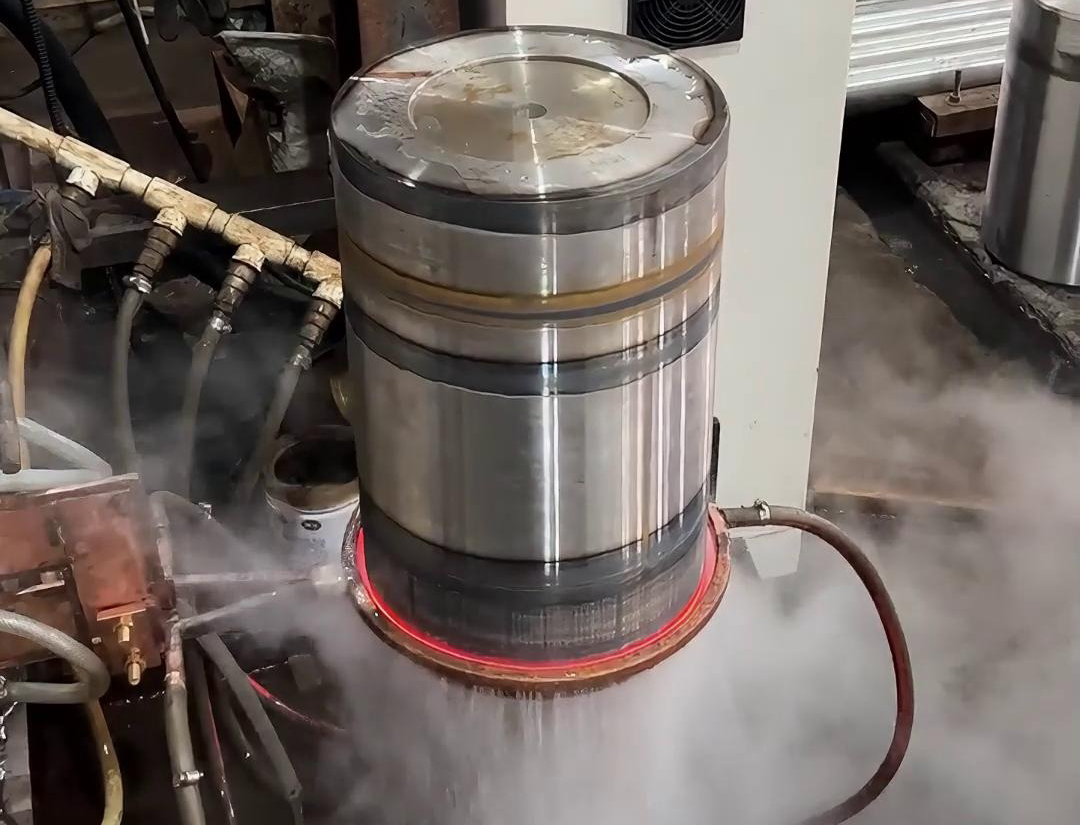
五、高頻淬火可能遇到的問(wèn)題及解決方法
- 淬硬層崩落:可能是由于淬硬層太深、冷卻速度太快或回火溫度低等原因造成的。解決方法包括縮短加熱時(shí)間、減少水壓并提高冷卻水的溫度、調(diào)整凸輪軸和感應(yīng)器的距離等。
- 局部熔化:可能是由于加熱溫度過(guò)高、凸輪軸沒(méi)有進(jìn)行旋轉(zhuǎn)式淬火或感應(yīng)器與凸輪軸之間的距離太近等原因造成的。解決方法包括縮短淬火時(shí)間、降低功率、用夾具讓凸輪軸旋轉(zhuǎn)著淬火等。
- 相鄰部位回火:可能是由于淬火部位之間的縫隙太小或感應(yīng)線圈與淬火部位沒(méi)有在相互對(duì)應(yīng)的位置造成的。解決方法包括在感應(yīng)器上安裝屏蔽性設(shè)備、調(diào)整感應(yīng)器和凸輪軸淬火部位的位置等。
六、高頻淬火的安全操作與維護(hù)保養(yǎng)
- 安全操作:操作人員應(yīng)接受專業(yè)培訓(xùn),了解設(shè)備的安全操作規(guī)程和注意事項(xiàng),確保在操作過(guò)程中的人身安全和設(shè)備安全。
- 維護(hù)保養(yǎng):定期對(duì)設(shè)備進(jìn)行維護(hù)保養(yǎng),包括清潔設(shè)備表面、檢查電氣元件和傳動(dòng)部件等,確保設(shè)備的正常運(yùn)行和延長(zhǎng)使用壽命。
綜上所述,凸輪軸高頻淬火是一種高效、精確的熱處理方式,能夠顯著提高凸輪軸的表面硬度和耐磨性。在使用過(guò)程中,需要注意工藝參數(shù)的選擇、可能遇到的問(wèn)題及解決方法以及安全操作與維護(hù)保養(yǎng)等方面的問(wèn)題,以確保設(shè)備的正常運(yùn)行和淬火效果的質(zhì)量。
|